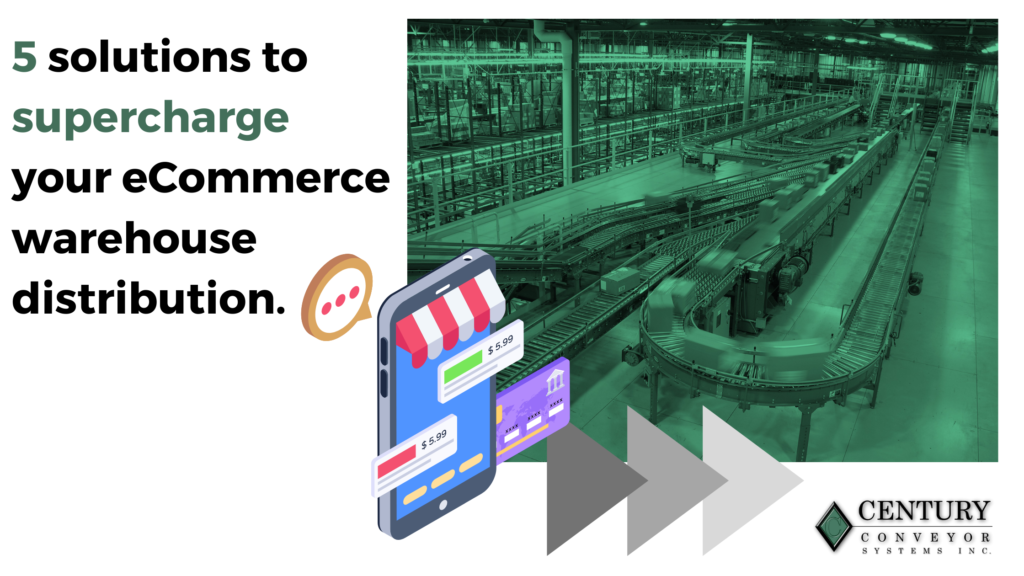
eCommerce warehouses have seen an explosion in demand recently, with consumer behavior pivoting greatly to online shopping. The ease of finding the exact item needed, and convenient purchasing options have made eCommerce outlets a popular platform for customers. Comparing Q3 2019 to Q3 2021 shows a whopping 45.6% increase in online sales (source), exacerbated by pandemic consumer buying behaviors. Every business wants a piece of the eCommerce pie, and many are pivoting to offer online shopping avenues, with no end to eCommerce growth in sight.
With that exponential increase in online sales, more and more warehouses are looking into eCommerce automation solutions that’ll meet expectations, reduce errors, and above all – fulfill orders rapidly. Some of the solutions used in eCommerce warehouses and DCs include:
- High output conveyance
- Quick scanning and sortation
- Automatic label print-and-apply
- Robotic picking
- Large SKU inventory solutions
Finding yourself in the same boat? With over 40 years of automation solution integration knowledge, and extensive experience designing systems for eCommerce clients, Century is acutely aware of which systems work best in an eCommerce distribution environment.
1. High output conveyance
Delivery expectations have greatly increased in recent years, primarily due to the prevalence of same or one-day shipping offerings online. Those expectations have extended to wholesaler clients, whose operations must match a competitive wholesale e-commerce landscape. Much like adjacent markets (third-party logistics, for example), automating order fulfillment is key to satisfying customers, while also offering an edge over the competition who don’t have quick shipping incentives.
A tried-and-true conveyor system is best suited for online order fulfillment. Depending on the size of the warehouse it’s installed in, and the product being transported, a conveyor system can include a variety of automation that’s designed specifically for your distribution center.
Simple and durable, a high output conveyor can achieve speeds over 50 cartons per minute and can last around 20 years (on average). Century has decades of experience with conveyor systems, and some of our largest integrations have been highly complex conveyor solutions. Here is one of our systems in action.
2. Quick scanning and sortation
The ability to rapidly and effectively sort your online orders is of paramount importance when operating an eCommerce distribution center. Even just one incorrectly sorted package can cause headaches, and with the ease of returns for consumers, it’s best to ensure the package is sent to the correct destination the first time around. Before sorting operations begin, correct scanning must take place. A scan tower is sensitive enough to capture the UPC code as it quickly passes by on the conveyor section. From there, a form of sortation diverts packages to the correct outfeeding line for loading.
- Tilt-tray
Tilt-tray sortation uses order consolidation chutes to sort items in a batch-pick environment. Cartons are scanned before being inducted onto a tilt-tray carousel, where it will sit on a moving platform until it reaches their destination chute. The tray will tilt either left or right depending on where it’s being sorted and slide down a chute onto a conveyor to be loaded.
Tilt-tray applications are effective for high-speed sortation.
- Cross-belt
Functioning similar to the tilt-tray, cross-belt sortation differs by using bi-directional belts to divert items into destination chutes. Packages are inducted onto the cross-belt conveyor carousel and sorted accordingly. Each belt section can hold one package, but multiple belt sections can be combined and used in tandem to divert larger items.
- Narrow-belt
A series of narrow belts, each with its own take-up, span the length of the conveyor. High friction divert wheels rise between the belts, diverting product to its destination.
Narrow belts are typically used for larger, heavier packages that need heavy-duty forms of sortation. Smaller packages would not be ideal for this application, as they would fall in-between the belting segments.
- Shoe Sorter
High-speed sorter utilizing aluminum slats that have plastic shoes that slide across them to divert cartons either left or right (bi-directional) to required sort destinations.
The advantage this provides over the similar functions of the tilt-tray is that the shoe is incorporated as part of the central induction conveyor. This eliminates the need for a separate sortation application, like the aforementioned tilt-tray carousel.
- Split-tray Sorter
Sometimes also referred to as a bomb-bay sorter, dual split tray sorters have the ability to sort two smaller items within the same tray, at higher throughput speeds.
Split-tray sections have a bottom platform that opens to drop items gently into chutes, totes, or cartons below. This method is space-saving, as the item discharge area drops below vs being conveyed.
- Swivel Wheel Sorter
Swivel wheel sorters utilize a platform of omni-directional rollers to divert items quickly. When a product reaches the divert, the wheels orientate to direct the item to its destination. This sortation method works best for systems that have a conveyor junction, rather than a gradual merge or curve.
- Push-tray Sorter
A high-speed sorter with tray segments utilizing a positive divert to gently push items or polybags off the tray and slide them into a sortation chute.
Depending on the dimensions of the parcel processed, each conveyor sortation method varies slightly, and one solution may work better than another one. It’s a function of careful engineering and planning to discover which one would work best. Regardless, any conveyor sorter will far exceed manual labor.
3. Automatic label print-and-apply
Affixing identifiable tags on packages is crucial to ensuring their deliverability. Scanners and sensors across the line depend on a readable tag for it to make it to its destination. Print and apply systems do exactly that. However, there are multiple systems depending on the identification process use and where the box must be marked. Applications can roll-on, wipe over, corner wrap, air blow, and stamp labels.
The direction the box must be scanned also plays a role in a solution selection, but it will outpace manual operations regardless. Automatically printing and applying labels maintains a consistent throughput rate across your system and provides an accurate and stable method of ensuring the correct package is labeled, decreasing the number of errors, returns, and items on a recirc line.
4. Robotic picking
Automating portions of picking operations with robotics is becoming a more commonplace implementation within eCommerce DCs. As technology advances, warehouse robots grow more accessible and inexpensive, making them a viable integration for any warehouse.
The most common warehouse robots are categorized into two applications. Automated Guided Vehicles (AGV) and Autonomous Mobile Vehicles (AMR).
AGVs and AMRs both provide a multitude of functions, typically moving items from one area of the facility to another, absent of human interaction. The difference between the two is in the way it senses the environment. AGV’s move by using a sensor that follows a set path (typically a form of sticker or tape on the ground). AMRs move by sensing objects around them, and learning an optimal path. In this sense, both have applications that one or the other is better suited to.
The prevailing advantage of AGVs and AMRs within eCommerce is minimizing, or even eliminating completely, employee movements. Instead of picking SKUs or cartons and transporting it themselves to induction operations, a nearby fulfillment robot can make that trip itself, saving precious time for the employee. Larger AGV and AMR systems can even retrieve, store, and transport pallets, minimizing manually operated forklift units.
For an eCommerce warehouse, robots prove effective when deployed strategically and in tandem with your warehouse staff. Century can source and implement AGV and AMR systems, engineered precisely for your eCommerce fulfillment and distribution. Got a few questions? Have a chat with one of our automation experts and we’d be happy to help out.
5. Large SKU inventory solutions
With the sheer amount of items available for customers to purchase online, it’s imperative to offer every variant of an item to a customer, because if it’s not exactly to their liking or specifications, they’ll purchase from somewhere else that has it in stock. This is especially important for fashion and apparel companies, because essentially every item needs to be in multiple sizes, colors, and styles. Besides having enough warehouse space and racking to store all these items, one automated solution has gained popularity recently for streamlining the picking of massive SKU catalogs.
Shuttle Systems
A shuttle system utilizes pick robots within a racking structure. When an order is being fulfilled, the robot navigates to the compartment where the item is held, retrieves it, and brings it to the worker’s pack station or an item dispenser receptacle. If your eCommerce warehouse operates a large catalog of items (for example, a shoe company that has multiple sizes, colors, brands, etc) a shuttle system will make quick work retrieving the indicated item for order fulfillment operations. One of the most well-known systems on the market today is Autostore.
Shuttle systems are modular, meaning that the structure can be designed according to your warehouse’s specification, the project budget, and the number of items you have in your inventory. Manual picking operations can be time-consuming the more products you carry, and with customer shipping expectations, expediting that process with a shuttle system will significantly decrease order fill times.